Increasing Performance of Tutco Process Heating Elements
People don’t give much thought to heating elements until there’s problem. Issues arise when the proper operating precautions are ignored, and processes go unchecked. Failed heating elements require significant maintenance issues and cause production process problems. Since heating elements are important components in many production processes, repeated failures can lead to unwanted downtime and monetary losses.
Preventive maintenance plans rarely included an electric process heater. However, heating components are equally important components in production processes. Unlike pumps, motors, blowers, and compressors, it’s assumed that heaters are designed to perform and withstand time. Heating components are denied attention because personnel assume that they do not require the same level of maintenance as other equipment. The lack of visible moving parts within air heaters components play a role in this thinking. However, heating elements expand and contract during temperature changes and power cycling. Many companies push heating element temperatures to increase production to improve time to market. The rapid temperature changes, and high temperature ramp rates exponentially decrease element life. All heating elements will degrade and fail over time. Maintenance is inevitable with any component, but there are ways to maximize element life, increase performance, and set life expectancy expectations.
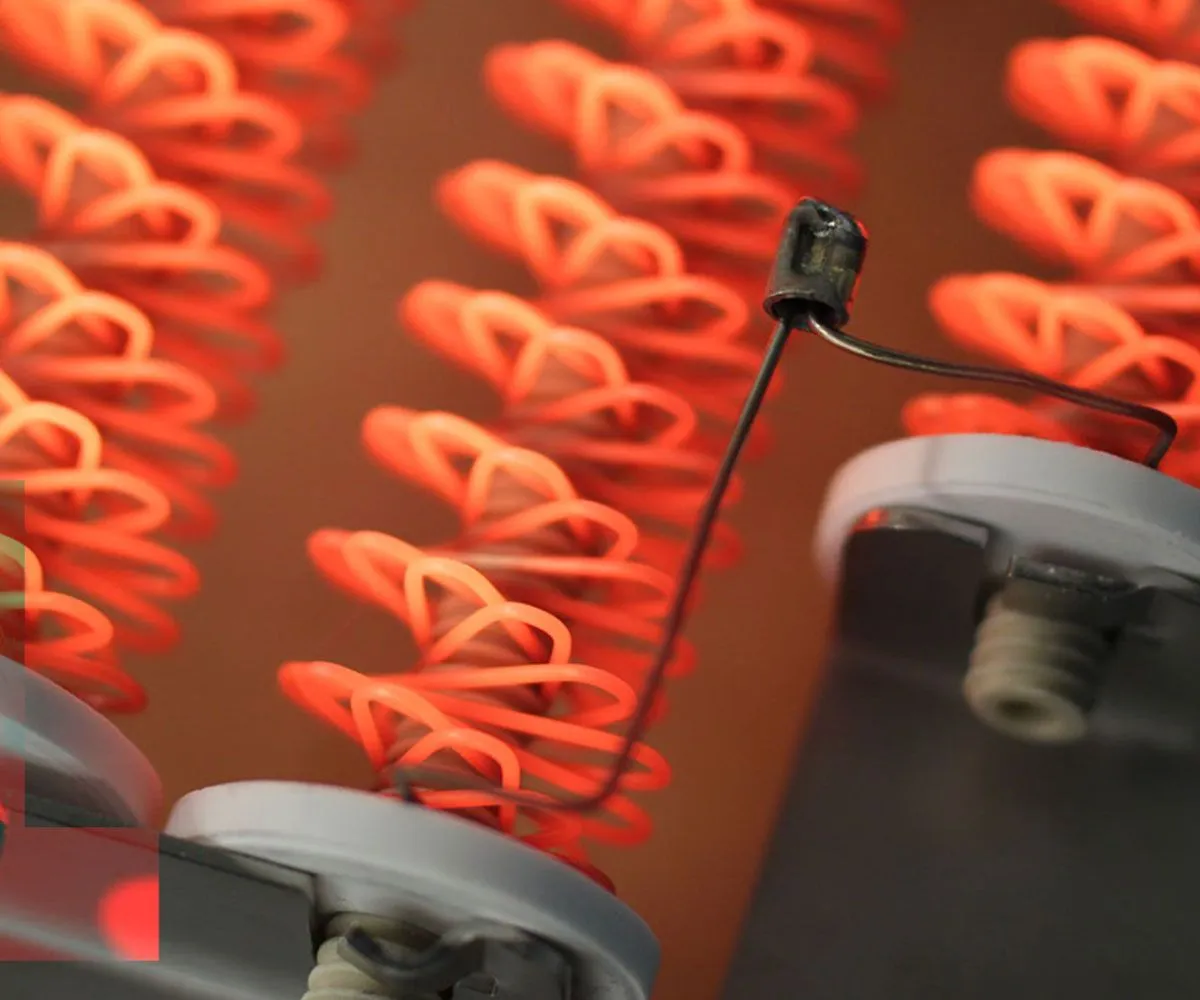
Eliminate contamination in the air stream
Contamination is a frequent cause of heater failure. The most common contamination is oil or moisture from compressed air lines. Sometimes contaminants can be conductive materials that inadvertently get sucked into and enter the airstream. Conductive materials will lead to arcing failures in the element windings so it’s very important to filter the air before the process.
Protect leads and terminations
Many heaters use fiberglass-insulated lead wires. The wire is typically at the cooler inlet end of the heater. It’s important to avoid temperatures above the rated insulation temperatures. If the insulation is damaged, the results could be exposed electrical wire. If leads are exposed to high temperatures, ceramic beads should be used to insulate the wire to avoid dangerous situations. When heaters are mounted on articulating or moving equipment, it’s important to rout, secure, and protect the wire with loom options to prevent damage.
Proper heater selection and sizing
Power should be matched to the application's actual load requirements to limit heater cycling. Heater voltage cycling reduces the lifespan of the element. The element expands and contracts while cycling on and off. Ensure an optimal fit between the heater and application to avoid air gap leakage and hot spotting that will lead to overshoot failures.
It’s also important to ensure the available supply voltage matches the heater's voltage rating. For example, if a heater is rated for 120V/1000W and is connected to a 240V supply, it will increase the current demands and the voltage would increase to 4000W. (Watts = Volts2 / Ohms) This can cause heater to fail and can cause damage the attached control equipment.
Grounding equipment
It is common sense and safe practice to electrically ground all equipment, including the heater. Grounding equipment helps protect personnel in the event of an electrical failure.
Prevent slow and excessive heater cycling
Heater failures are often caused by excessive temperature cycling. A cycle rate that creates full expansion and contraction of the heater resistance wire exponentially reduces the life of the element. The most effective way to minimize heater element temperature cycling is to use solid state relays (SSRs) and SCR power controllers coupled to PID temperature controllers. Using a temperature controller with 200 millisecond (0.2 Seconds) or faster cycle time, ensures fast responses and smoother cycling to changing temperature conditions. Also be sure the Power Controller (SCR) or Solid-State Relay (SSR) is equally fast at regulating the AC voltage to the heater. Solid state switching devices rapidly cycle power. Rapid power cycling dramatically reduces heater element wire temperature excursions and substantially extends heater life.
Ensure that heater sheathing materials are compatible with the application
Increasing air flow and turbulence across the heater elements means better heat transfer and higher watt density values. It’s critical to ensure the right materials are used for high temperature applications. The operating temperature limits heater materials to stainless steels and other higher temperature metal alloys. Proper heater selection ensures heat transfer and minimizes overshoot. The internal insulator material choices are also important considerations.
Make sure the air is on before applying voltage to the heater
Air passing through the heating element is required to cool the element. Without air, the heating element can rapidly overheat. Overshoot will quickly damage the element and insulation materials without air flow. Make sure the air is on before applying voltage to the heater and leave the air on to cool the element and heater materials after the process is shutdown.
Temperature control and setting limits
Matching the appropriate control panel to the heater is imperative to heater performance and life. Use control panels with multiple thermocouples to measure the air temperature close to the heating element as high limit protection. Use the other thermocouple as the process temperature control adjustment. Properly insulate all heater enclosures, piping and process enclosures to maintain temperatures. Allow time to ramp up to process temperatures. Set appropriate ramp rates to minimize stress to the element.
Manage maintenance schedules and heater element life
Very few companies stock spare heating elements on-site. Know lead times to get a new replacement product. When purchasing a heater, ask about service records and time to replace / rebuild. Work with a manufacturer that regularly stocks replacements and has great customer service. Train with experts on the control and setup of the heater. Choose solutions that have field replaceable element options when possible. Look for products with built in protections and multiple thermocouples for protecting the heater. Purchase matching control panels. Compare warranties and ask about common pitfalls. If custom solutions were built, ask about maintenance schedules. Create a maintenance schedule and record the element replacements. Some custom heaters can take longer than 6 weeks to rebuild. If a heater fails during operation, it can be a significant financial burden. Although heaters are made to endure wear and tear, problems can still arise. Without a spare on-site, the risk of unplanned down time is higher. Avoid downtime by having spare elements or heaters to avoid risks. Understand what caused a premature failure. Don’t connect and run another heater until the problem is identified and fixed.